Improving Employee Health, Safety, and Security: A Generalist’s Guide to Speciality Skills
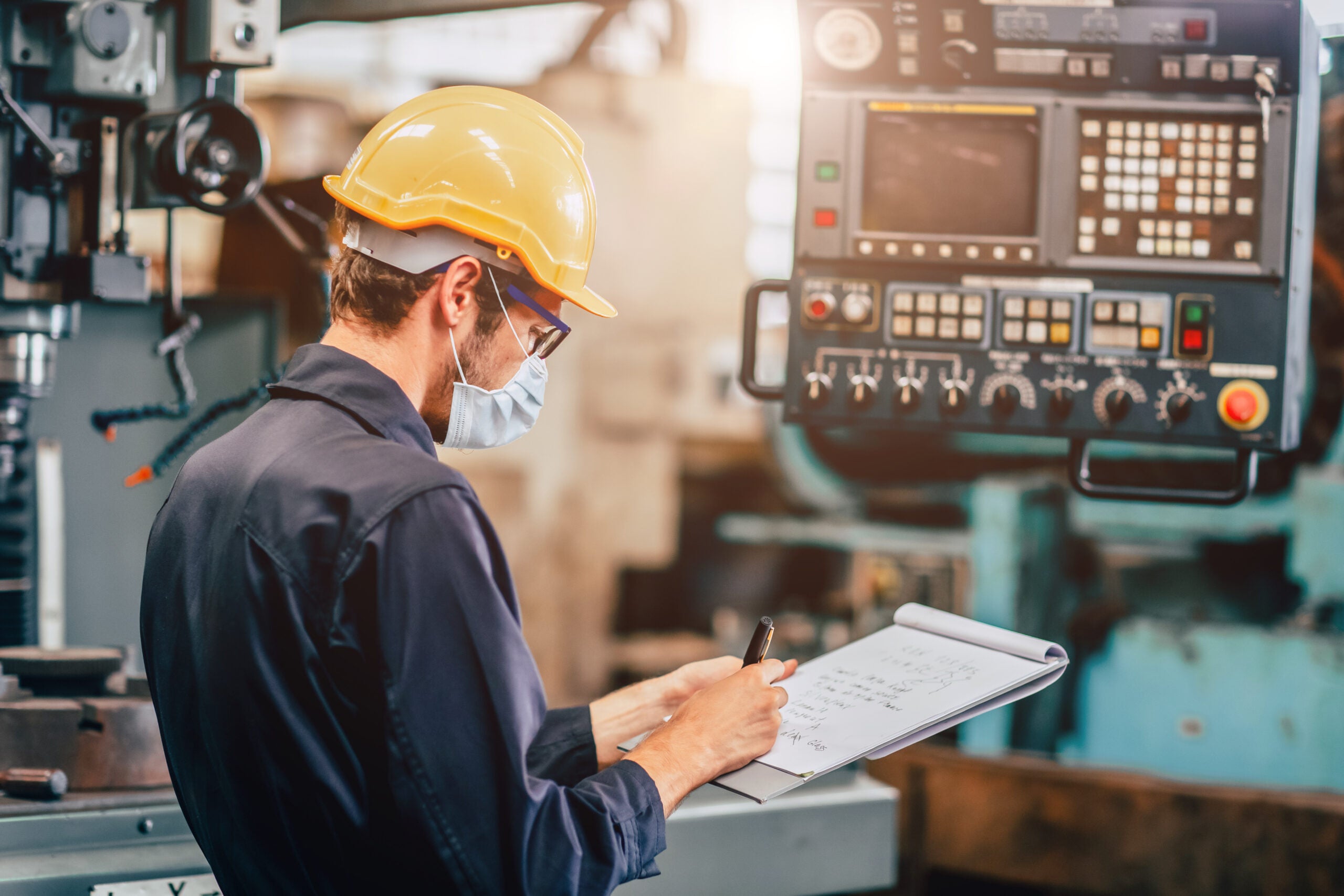
The online five-day Fundamentals of Industrial Hygiene course teaches the foundations of safety practices and professions: anticipating, evaluating, preventing, and controlling workplace hazards. These skills are crucial given that work-related injuries and illnesses significantly impact employee productivity and employers’ bottom line. The course serves as a solid entry point to or a refresher in industrial hygiene. After all, even for those well-versed in the industry, changes in artificial intelligence, equipment, and other forms of technology are shifting the way hazards are evaluated and controlled. The COVID-19 pandemic has also changed many ventilation and indoor air quality testing protocols.
Louis J. DiBerardinis, M.S., the program co-director and instructor of industrial hygiene in the Department of Environmental Health at Harvard T.H. Chan School of Public Health, says that in addition to foundational knowledge, Fundamentals of Industrial Hygiene provides participants with a unique layer of expertise, enhancing one’s value to one’s organization and aiding in potential career advancement.
Many professionals beyond industrial hygienists—including those in manufacturing, pharmaceuticals, biotech, and research—can also benefit from fundamental industrial hygiene skills. “The course allows you to improve skills in your specific area while also allowing you to expand your horizons,” says DiBerardinis. For example, while a radiation safety officer may be highly skilled in their particular role, if their knowledge is expanded to include chemical or biological hazards, they may be more valuable to a company—and in a better position to advance, DiBerardinis says.
He adds that broadening one’s skills allows workers to do jobs that companies may otherwise have to outsource, improving productivity and efficiency and reducing the time spent on issues. The course covers everything from ergonomics and personal protective equipment to respiratory protection, ventilation, noise reduction, sampling and instrumentation, and more.
A new crop of skills can also improve communication and confidence in workers. “Sometimes folks are by themselves managing different programs and hiring consultants. They need to know how to communicate with consultants for specific needs and understand what services consultants can provide—not just rely solely on bringing in an outside expert and letting them run wild through the company,” explains John M. Price, Ph.D., a retired instructor at the Harvard T.H. Chan School of Public Health and the Northeastern University Departments of Chemical Engineering and Bioengineering.
He says that bolstered knowledge of safety programs and needs can work to fine-tune the services provided. In short, participants are better able to accurately and immediately improve employee health and safety at their organizations.
There’s a bigger picture benefit to this, too: “It all goes a long way to having employees feel satisfied that the company is concerned about their health and safety and that someone can respond immediately,” says DiBerardinis.
That’s critical as health, safety, and environmental issues can also negatively impact public perception of an organization.
For those in the industry, the course is also a pathway to becoming certified in industrial hygiene someday if that is a future goal.
This summer’s course will feature new highly-respected speakers in various fields—each of whom will address emerging issues in their particular industry—providing a toolkit of case studies, references, and videos and the opportunity to problem-solve real-world issues in the course.
While the course is centered on rigorous learning, it also includes a live working group of peers hosted virtually. DiBerardinis says, “People can gain the wisdom of not only the instructors but all others in the course.”